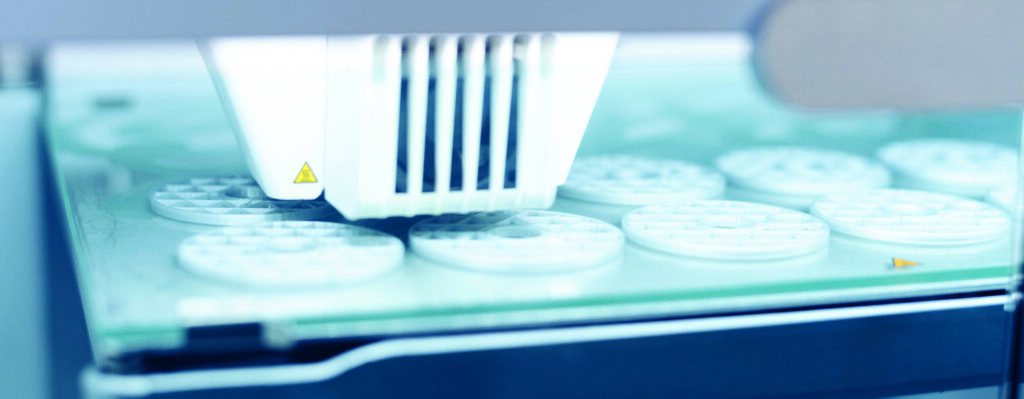
Rapid Prototyping Verfahren - Additive Fertigung
Rapid Prototyping Verfahren, Additive Fertigung bzw. additive manufacturing (AM) oder auch generative Fertigung sind Bezeichnungen für den 3D-Druck. Letztlich stehen dahinter unterschiedliche Verfahren zur schichtweisen Erzeugung von Körpern, die zuvor als digitales 3D-Modell erstellt wurden.
Jedes 3D-Druck Verfahren hat seine individuellen Vor- und Nachteile. Das Innovationspotential ist groß und täglich kommen neue Rapid Prototyping Verfahren oder Abwandlungen bekannter Verfahrenstechniken hinzu. Da kann man schnell mal den Überblick verlieren. Im Folgenden stellen wir Ihnen darum die gängigen 3D Druck Verfahren mit Stärken und Schwächen übersichtlich da. Finden Sie so heraus, welches für Ihre Anwendung geeignet ist.
Sie sind sich unsicher, ob Sie das richtige 3D-Druck Verfahren für Ihre Zwecke gefunden haben? Fragen Sie uns!
Das FDM 3D Druck Verfahren (Fused Deposition Modeling) ist eines der gängigsten Rapid Prototyping Verfahren zur Herstellung von 3D Druck Teilen. Dabei wird ein Kunststofffaden (Filament) durch eine heiße Düse (Extruder) gepresst. Das digitale 3D Druck Modell wird zuvor durch ein Programm (Slicer) in viele Schichten zerlegt bzw. geschnitten und diese Schichten dann durch den FDM Drucker nacheinander, übereinander auf ein Druckbett aufgebracht. Das so entstehende 3D Druckteil ist unmittelbar nach Abschluss des 3D Druck Prozesses nutzbar.
Die Möglichkeiten der Formgebung sind beim FDM 3D Druck nahezu unbegrenzt. Jedoch gibt es Einschränkungen. Um größere Überhänge zu ermöglichen, die sonst „in der Luft“ gedruckt würden, werden Stützstrukturen (Support) benötigt. Sie entstehen während des Drucks aus dem gleichen oder einem anderen Material und müssen anschließend manuell entfernt werden.
Der 3D Druck im FDM Verfahren bietet einige Vorteile gegenüber anderen 3D Druckverfahren.
Mit FDM Druckern kann eine große Vielfalt an Kunststoffen verwendet werden. Der verwendete Werkstoff lässt sich beliebig und ohne großen Aufwand wechseln. Ein paar geübte Handgriffe und schon kann es mit Ihrem Teil losgehen.
3D Druck im FDM-Verfahren
Die Stereolithografie, auch SLA Verfahren oder SLA Druck genannt, ist ein Rapid Prototyping Verfahren, bei dem Kunststoffe Schicht für Schicht mit Hilfe von UV Laser Belichtung zu einem Bauteil ausgehärtet werden. Hierbei bewegt sich eine Plattform innerhalb eines Beckens voller Flüssigkeit stufenweise nach unten. Ein Rakel wischt über die Oberfläche der Plattform bzw. des Bauteils auf der Plattform und sorgt so für eine gleichmäßige Schichtdicke. Anschließend fährt ein UV Laser über einen beweglichen Spiegel die auszuhärtenden Stellen detailgenau ab und verhärtet das Material.
Bei der zur Stereolithografie verwendeten Flüssigkeit, die auch Resin genannt wird, handelt es sich um einen flüssigen Kunststoff aus Einzelmonomeren wie Acryl- oder Epoxidharz. Die einzelnen Bestandteile im Harz reagieren durch die Belichtung mit dem UV Laser zu einem Polymer. Durch mehrmaliges Wiederholen dieser Schritte entsteht ein 3D Druck Bauteil.
Je nach Geometrie des Bauteils werden besondere Stützstrukturen im 3D Modell eingefügt und dann gedruckt, um eine ausreichende Haftung am Druckbett zu gewährleisten oder Überhänge zu realisieren. Diese müssen im Anschluss mechanisch entfernt und das Bauteil mit einem Reinigungsmittel wie Isopropanol von überflüssigem Harz befreit werden. Abhängig vom verwendeten Material und Einsatzzweck ist es teilweise notwendig, ein SLA 3D Druckteil noch unter UV Strahlung oder in einem Ofen aushärten zu lassen.
Mit steigender Technologisierung ist die Stereolithografie ein wichtiges Verfahren zur Fertigung von hochpräzisen Bauteilen und Prototypen mit einer glatten Oberfläche geworden. Komplizierte Geometrien können mit hoher Genauigkeit problemlos 3D gedruckt werden. Die Anwendung des SLA Verfahrens ist durch die Einschränkungen in der Materialauswahl recht begrenzt. Bauteile, die mit Hilfe von Stereolithographie hergestellt sind, sind meist weniger UV-beständig und recht spröde im Vergleich zu Bauteilen, die mit dem FDM Verfahren hergestellt wurden.
Stereolithografie - SLA 3D Druck
Ähnlich zur Stereolithographie (SLA) wird auch beim Selektiven Lasersintern (SLS) das Ausgangsmaterial mithilfe eines Lasers erhitzt, um das Bauteil zu formen. Im Gegensatz zum SLA Verfahren werden beim SLS Verfahren pulverförmige statt flüssige Materialien verwendet. Hierbei handelt es sich um eine weitreichende Auswahl an Metallen, Keramiken, Kunststoffen oder Formsanden.
Das Pulver wird mit einem Rakel gleichmäßig in dünnen Schichten über den Druckraum verteilt. Anschließend fährt der Laser mithilfe eines Umlenkspiegels die im Voraus festgelegten Vektoren ab und erwärmt das Material an diesen Stellen bis knapp unter bzw. genau auf den spezifischen Schmelzpunkt. Das Pulverbecken im 3D Drucker wird dazu vorgeheizt und der Laser muss nur noch einen Restbetrag an Energie zum Schmelzen des Werkstoffs aufbringen. So verdichtet sich das Pulver zu einem homogenen Bauteil und es entstehen hochpräzise 3D-Drucke.
Beim SLS Druck dient das nicht benötigte Pulver gleichzeitig als Stützmaterial des 3D gedruckten Bauteils. Das ermöglicht einen hohen konstruktiven Freiheitsgrad und so sehr komplexe Bauteile zu drucken. Das Restmaterial kann im Nachhinein zu einem hohen Anteil wiederverwendet werden. So müssen keine oder nur sehr wenige Stützstrukturen gedruckt und anschließend entfernt werden. Das spart Material, Zeit und damit Kosten.
Nach dem 3D Druckvorgang müssen die Bauteile gleichmäßig abkühlen, um ein Verziehen des 3D gedruckten Werkstücks beim spontanen Abkühlen zu verhindern. Dazu verweilt es, abhängig von der Bauteilgröße, noch eine Zeit lang innerhalb des Druckers. Im Anschluss werden die fertig abgekühlten Teile in einer Reinigungskammer mit Hilfe von Druckluft oder einem Strahlverfahren vom überflüssigen Material gesäubert.
Die Struktur des fertigen 3D Druckteils ist leicht porös. Das ist vorteilhaft für den Leichtbau, aber nachteilig für die Belastbarkeit. Es gibt eine Reihe von Wärmebehandlungen und andere Nachbearbeitungen, die es erlauben die Festigkeit und Belastbarkeit des 3D gedruckten Bauteils nachträglich zu steigern.
Die Oberfläche der fertigen Teile ist zunächst rau und abhängig von der Korngröße des verwendeten Pulvermaterials. Für die Oberflächenveredelung gibt es eine Fülle an Verfahren, so dass auch 3D Druckteile mit sehr glatten Oberflächen im SLS Druck Verfahren möglich sind.
Selektives Lasersintern – SLS 3D Druck
Das Selektive Laserschmelzen, kurz SLM, oder auch Laser Pulverbett Fusion (LPBF) ist ein weiteres 3D Druck Verfahren auf Basis eines Pulverbetts und damit dem SLS-Verfahren sehr ähnlich.
Das SLM Verfahren wird zur additiven Fertigung von stark beanspruchten Metall Werkstücken eingesetzt, die eine hohe Genauigkeit verlangen. Sie können sich mit diesem Verfahren ein Werkstück aus Metall 3d drucken lassen, dass voll funktional und damit sogar für Serienteile geeignet ist. Wie bei allen additiven Verfahren mit Pulverbett, wird auch beim SLM-Verfahren das Bauteil über eine dünne Schicht Pulver, welches von einem Laser erwärmt wird, nacheinander aufgebaut, indem die Baukammer um den jeweiligen Betrag der nächsten Schicht absinkt. Im Gegensatz zum selektiven Lasersintern wird das Material bis über den Schmelzpunkt erhitzt und somit komplett geschmolzen. Dadurch erhält man Bauteile, welche ein Gefüge ähnlich dem von Gussteilen aufweisen.
Da bei diesem Verfahren ausschließlich Metall- bzw. Keramikpulver zum Einsatz kommen, muss eine Schutzatmosphäre (meist Argon oder Stickstoff) innerhalb der Baukammer geschaffen werden. Diese verhindert, dass die Struktur des Werkstücks durch den Sauerstoffanteil in der Luft verunreinigt wird und es zu Fehlern in der Struktur des Werkstücks kommt.
Je nach Struktur des zu druckenden Objektes, kann ein Einsatz von Stützstrukturen nötig sein. Diese erfüllen bei diesem Verfahren nicht nur den Zweck das Bauteil auf der Grundplatte zu verankern, sondern sie dienen ebenfalls zur Wärmeableitung, welche durch den teils hohen Temperaturunterschied der neuesten Schicht zu bereits gedruckten Schichten und damit zusammenhängende Spannungen ausgleichen kann.
Nach Abschluss des Druckprozesses lässt man die Bauteile zum Abkühlen innerhalb der Anlage verweilen. Anschließend wird überschüssiges Pulver, welches fast vollständig wiederverwendet werden kann und Stützstrukturen manuell entfernt. Dafür ist für gewöhnlich eine separate Reinigungskammer notwendig. Die Oberfläche ist ähnlich wie bei Lasersintern meist rau und bedarf ein Nachbearbeiten der fertigen Teile.